在半导体制造的发展历程中,光刻技术以其对摩尔定律的执着追求而著称。该技术遵循瑞利判据的数学模型,即:
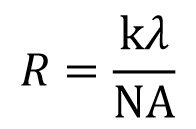
其中 R 为分辨率,k 为工艺因子,λ 为曝光波长, 为数值孔径。简单说说影响这几个因子:曝光波长 λ :0.1μm~90nm使用193nm 光源,通常来说越小越好;
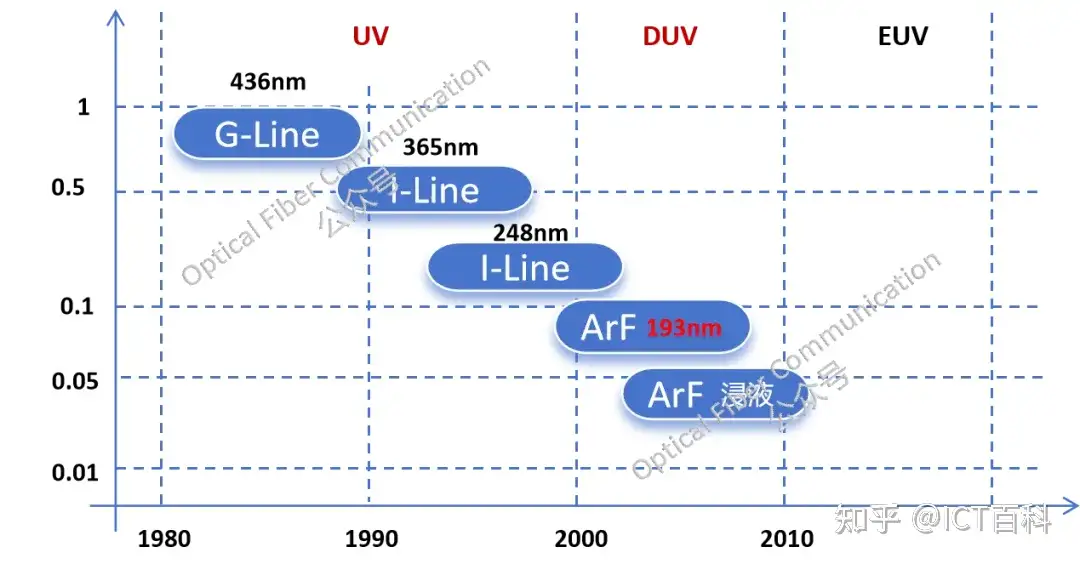
工艺因子 k:通常介于0.25到0.5之间,取决于光刻工艺的复杂性和所需的成像质量,越小越好;数值孔径 :镜头的数值孔径,越大越好;针对上面这些参数的通过不断优化,特别是通过减小 λ 和增大 ,以及光刻胶工艺等共同作用下降低 k 因子,在给定的波长下,光刻技术能够实现更高的分辨率。比如说在波长 λ 为 193 nm时,通过ArF(氟化氩)干法光刻技术,就可以实现 65nm半导体制造量产。
从公式可以看出,波长越短,光刻的就越精细,为了实现更高分辨率,难道我们就不能继续降低波长 λ ?对此,基于氟气准分子激光的输出波长特性,工程师将 157nm 波长做为下一代曝光波长的可选项。但是这个波长的光穿透力不足,需要改进光罩和镜头技术。同时,由于氧气会吸收该波长的光,必须使用氮气等非吸收性气体来替代,以避免介质中的吸收问题。因此, 157nm 波长的光刻技术没有成为主流。
那怎么办?
这时候 ASML 和台积电另辟蹊径,提出难道我们一定要执着于干式介质?
台积电发现 193nm 波长的光线经过水折射后,波长变为 132nm,直接跳过 157nm 波长。这就是浸润式光刻的基础原理,曝光介质是水,其曝光设备被称之为 i-ArF。在当时而言,与干式介质相比,浸液式ArF光刻技术的潜力可以实现从 45nm 到 32nm 乃至 22nm 技术节点的跨越。
PS:这里稍微解释一下啥叫干式介质,很简单指的是光刻机中不使用液体介质,而是使用气体。比如说 ArF(氟化氩)干法光刻技术中直接使用的是空气,其曝光设备被称之为dry-ArF(d-ArF)。
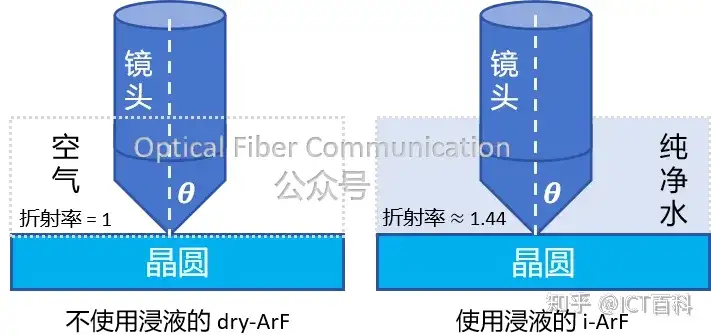
在浸润式光刻技术中,在外表看来我们是将波长变短,但其实只是利用光的折射定律,光的波长因液体的存在而等效地缩短,本质上还是提高数值孔径 ,它也介质的折射率有关。
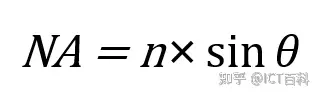
结合上面的图,水的折射率约为1.44,当θ(光线入射到光学系统孔径边缘的角度)大于70度以上时,数值孔径 NA 的值大于 1 。这里我们可能会想到,是不是NA越大就越好?理论上,NA 越大,光刻机的分辨率越高,能够制造的特征尺寸越小。但实际上并不是这样的,随着 NA 的增加,另一个问题就会出现,即焦深(DOF:Depth of Focus)带来的限制。
焦深是指在光刻过程中,硅片相对于光刻机镜头可以偏离理想焦点位置的允许范围。
焦深与数值孔径 NA 的公式如下:
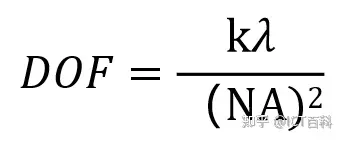
较大的焦深意味着在较大的垂直偏差范围内仍能保持清晰的图像。从上面公式可以得出 DOF 与 NA的二次方是成反比的,随着 NA 的增大,DOF 将急速变小,也就是说刻机镜头可以偏离理想焦点位置的允许范围越来越小,即 NA 增大,分辨率提高,焦深变小。焦深的变小双导致对硅片平整度和对准精度的更高要求,平坦度CMP可以参考:为什么需要CMP工艺?,什么是减薄,与 CMP,磨削研磨又有什么不同?
不禁思考,浸液的极限是多少?而在我看来,之前有说开发更高折射率的浸液,或许并不是一条正确的技术路线。
最后简单聊聊基于浸液式光刻技术的产品:
在2005年6月底,尼康公司发布了其先进的光刻系统 “NSR-S690B”。该系统的数值孔径(NA)达到了 1.07,能够实现 55nm 工艺的量产和 45nm 水平研发的光刻需求。紧接着尼康公司的发布,ASML公司于 2005 年 7月初发布了其浸液式光刻系统 “XT:1700i”,该系统的NA高达1.2,可支持 45nm 的光刻工艺。
值得注意的是,也是回答上面的问题(浸液的极限是多少?),对于更小特征尺寸的追求已经超越了浸液式光刻技术的物理极限。因此,极紫外光(EUV)光刻技术被开发出来,用于实现更小的特征尺寸,如7nm、5nm,3nm甚至更小的工艺节点。
感谢阅读!